2014年硅氟產業發展交流合作大會上,楊曉勇說: “2014年3月18日,美國一家網站公開發表了鮑爾州立大學化學系研究人員的研究成果:在室溫下采用電化學的方法,以正己烷作溶劑,將硅石與甲醇反應,直接獲得D3、D4和D5硅氧烷單體混合環體,甲醇轉化率幾乎是100%,而反應電壓只有2.7~3V。我看到這條消息有些震驚,這個技術一旦開發成功,將給全球有機硅產業帶來革命性變革。新工藝直接用硅石原料,省去了電解還原金屬硅的步驟,這樣就能大大降低有機硅單體合成的能源消耗,成本也會隨之大幅降低。如果未來三五年這一技術實現工業化,對我國現有的機硅單體生產企業將是巨大的沖擊!
事實上,自聚硅氧烷作為新型材料得到廣泛應用之后,采用二氧化硅直接合成聚硅氧烷的科學探索就一直沒有停止過,最早采用此方法合成聚硅氧烷研究文獻可以追溯到60年代,但難以實現工業化生產。美國、日本和歐洲的一些大學和研究機構也將此作為化學工業可持續發展的重點課題。
傳統的有機氯硅烷合成是采用金屬硅和氯甲烷作為主要原料,而金屬硅的生產原料就是自然界的石英(二氧化硅)。由石英制造金屬硅采用碳還原法,即:
SiO2 + C = Si + CO2
我們知道Si-O鍵能為422.5kJ/mol,可想而知該反應所需的能耗巨大,能耗占到金屬硅成本的70%左右,目前生產1噸金屬硅的電耗在13000kwh – 15000kwh.。
金屬硅與氯甲烷合成為混合甲基氯硅烷后,通過分離技術得到純凈的二甲基二氯硅烷,再通過水解、裂解(詞條“裂解”由行業大百科提供)工藝,得到我們需要的DMC。這個過程同樣能耗巨大,而且裝備投資密集,是目前基礎工廠的主要能耗單元。
可想而知,如果采用石英直接合成DMC能實現工業化,對有機硅行業而言將是一場顛覆性的革命,就像微信顛覆了傳統的短信、圖片、語音等信息傳遞技術一樣,必將改變有機硅行業的現有格局,引發全球有機硅領域內的新一輪產業升級。
那么,我們離二氧化硅直接合成聚硅氧烷還有多遠?
現在,讓我們先回顧一下有機硅工業的發展簡史:
1941年,Rochow發明了直接法合成甲基氯硅烷,并申請了專利保護;緊接著Muller也在自己研究成果的基礎上,申請了直接法專利。
943年,Dow化學與Corning玻璃公司合資成立了Dow Corning公司。采用格利雅法生產有機氯硅烷,進而生產聚硅氧烷。
1947年,General Electric 公司成立,并采用直接法生產有機氯硅烷。至此Rochow直接法得到了工業應用。
1951年—1960年,德國瓦克、拜耳,法國羅納普朗克,日本信越化學,美國聯合碳化(詞條“碳化”由行業大百科提供)物均采用直接法工藝生產甲基氯硅烷。
直到上世紀70年代初期,發達國家的直接法合成甲基氯硅烷生產工藝趨于成熟,同時,聚合物研發和應用成果頻出,有機硅產業化、規;母窬珠_始顯現。
古語說:溫故而知新。對于直接法合成甲基氯硅烷工藝而言,從申請專利到工業化試生產用了六年的時間,到工業化成熟并形成規;昧私30年的時間。
我國的有機硅工業起步于1952年,北京化工試驗所(沈陽化工研究院前身)采用格利雅法生產有機氯硅烷。
1956年,沈陽化工研究院成立,開始直接法合成甲基氯硅烷試驗。
1958年,沈陽化工研究院、北京化工研究院和吉化公司開始建設直接法合成甲基氯硅烷實驗性工業裝置。
上世紀70年代,以吉化、北二化、星火為主體的企業,陸續開始進行百噸級、千噸級的直接法氯硅烷合成工業裝置試驗和生產。
1991年,星火萬噸級有機硅單體工業性試驗裝置投產。
1998年,星火萬噸級有機硅單體裝置正常生產。
2004年,星火5萬噸/年有機硅單體裝置投產,并達到設計指標。
對于中國有機硅單體行業而言,從研究開發到形成產業化、規;昧私50年的時間。當然,這里有當時的社會、政治和文化教育等多從背景的影響。
在信息高度暢通、科技高度發展、人才高速流動的今天,很多的科技成果產業化的案例告訴我們:一個科研成果的工業化取決于這個領域內的工程化技術的沉淀,取決于專業人員的素質,更取決于企業決策者敢于冒險的精神。
現在,鮑爾州立大學的成果還未完全公開,何時實現工業化還有待了解和分析。但我覺得,國內的有機硅單體生產企業不必過度對此憂慮,把現有的裝置開出水平,把現有的技術升級到一個更高的水平,實現企業管理、技術、效益的持續進步才是當前的大事!就辍

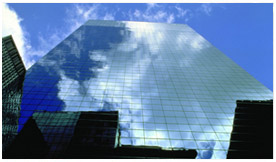
姓名:何永富
職位:杭州之江有機硅化工有限公司董事長
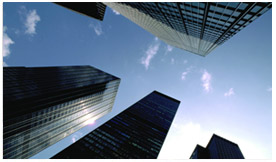
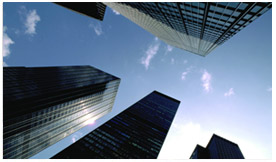